Soudage au MIG

Le soudage à l’arc MIG/MAG avec fil continu est le procédé de soudage lors duquel de la chaleur est générée par un arc qui se forme entre le métal d’apport et la pièce à souder. Le métal d’apport assure la fonction d’électrode tout en alimentant le joint. C’est-à-dire que le passage du courant fait fondre le fil et le soudeur introduit celui-ci dans le joint en appliquant de la chaleur à l’aide d’une torche. Le soudeur utilise autant de fil que nécessaire pour continuer le soudage.
La contamination du bain de fusion doit être évitée, car elle peut entraîner une diminution de l’intégrité de la soudure et une augmentation des coûts de nettoyage après le soudage. Les mesures de protection comprennent l’écoulement de gaz de la torche (soudure sous protection gazeuse) ou l’utilisation de fil fourré (soudure sans protection de gaz). Le fil fourré est également utilisé pour les électrodes enrobées.
Transfert d’arc pulsé
Les générateurs de soudage à commande électronique peuvent gérer le processus de soudage par fil en continu en modulant le courant. Par conséquent, ils peuvent utiliser des formes d’onde spéciales pour assurer un transfert régulier du métal, indépendamment de la chaleur fournie au bain et de l’apport de chaleur.
La figure 1 représente la forme d’onde la plus simple pour le soudage avec transfert d’arc pulsé. Lorsque des formes d’ondes simples sont utilisées, le soudeur module le courant électrique entre une valeur de base et une valeur de crête. La valeur de base est suffisante pour maintenir l’arc allumé. Lorsque la valeur de crête est atteinte, une goutte de fil fondu se détache et forme la soudure lorsqu’elle se pose dans le joint. Le facteur d’apport de chaleur est évaluée en fonction du courant efficace; cette valeur est normalement affichée sur l’instrument, sur la machine ou peut être mesurée à l’aide d’une pince de courant.
Le soudage à l’arc pulsé engendre une pénétration du dépôt directement synchronisé avec le courant de crête. En conséquence, l’apport de chaleur est plus faible puisqu’il est calculé en fonction du courant efficace plutôt que des valeurs de base ou de crête.

Le soudage à l’arc pulsé est fréquemment utilisé pour assembler des tôles minces, principalement lors du travail avec des matériaux particulièrement sensibles aux effets thermiques du soudage (aciers inoxydables, alliages non ferreux). Le soudage à l’arc pulsé réduit le risque d’inclusions, en raison du courant de crête, et de dépassements, causés par la réduction de l’apport de chaleur. C’est pourquoi cette méthode est souvent utilisée pour souder des alliages légers. Le soudage à l’arc pulsé de l’aluminium s’est amélioré grâce à l’introduction récente de programmes spéciaux liés à l’exécution de la première passe, du brasage, au confinement des fumées et du bruit de soudage, et à l’élimination du risque de porosité accrue après soudage.



PARAMÈTRES DE SOUDAGE
Métal d’apport
La qualité de la soudure dépend largement du choix du métal d’apport. Malheureusement, le fil de soudure se détériore peu à peu avec les années, ce qui entraîne des soudures de très mauvaise qualité. Lorsqu’un fil de qualité inférieure est utilisé, le cordon de soudure noircit et devient contaminé par des inclusions difficiles à enlever pendant le processus de nettoyage. La couleur du fil utilisé pour le soudage détermine également la coloration du cordon de soudure. Si le fil est foncé, le cordon de soudure le sera aussi. Le processus de fabrication des fils est donc tout aussi important. On obtient un fil de haute qualité par un processus d’étirage, une finition satinée et un double processus de nettoyage électrochimique. Le procédé de finition satinée sert à réduire la résistance au frottement du fil lorsqu’il traverse le conduit en plastique pendant le soudage. Le fil glacé a remplacé l’ancien fil blanc brillant puisqu’il avait une très haute résistance de frottement.
Un double nettoyage du fil augmente les coûts de production de 30 % par rapport au processus d’étirage normal. Très souvent, cette dernière phase est laissée de côté pour minimiser les coûts. Le fil reste donc graisseux, couvert de résidus de grains et d’huiles lubrifiantes utilisés dans le processus d’étirage. Pendant le soudage, ces résidus provoquent de la combustion qui engendre des brûlures et un noircissement le long du cordon de soudure. Des silicates se forment le long du cordon durant le processus de soudage, ce qui rend le processus de nettoyage électrochimique très difficile.
Le silicium présent dans la composition chimique du matériau d’apport est responsable de la création de silicates pendant le processus de soudage. La quantité maximale de silicium permise dans le fil est de 1 %. Celui-ci est ajouté aux éléments d’alliage, car il augmente la flexibilité et la maniabilité du fil, et donc, la vitesse d’étirage. Ces silicates ne peuvent pas être retirés du cordon, mais peuvent être réduits pendant le soudage. Les techniques pour réduire les silicates incluent :
- L’utilisation d’un fil à faible teneur en silicium;
- La diminution de la taille du cordon de soudure;
- L’utilisation d’un courant électrique faible;
L’utilisation de fils qui contiennent un pourcentage élevé de silicium augmente la probabilité de dépôts de silicate sur le cordon de soudure. Cette probabilité augmente proportionnellement à la taille du cordon de soudure. Lorsqu’un courant inutilement élevé est appliqué, la concentration de silicate augmente énormément, ce qui réduit les propriétés du matériau soudé. La décision d’augmenter le courant est très souvent motivée par le désir d’accélérer la production. Cependant, cela n’a pour effet que de produire des soudures de moindre qualité et compromettre la fiabilité du produit fini dans son ensemble.
Gaz protecteur
La quantité de gaz de protection qui s’échappe de la buse est un autre facteur important du processus de soudage. Si le débit est trop faible, le gaz ne protégera pas suffisamment le bain de fusion. Un débit de gaz trop élevé provoquera de la turbulence qui permettra à l’oxygène contenu dans l’air de réagir avec le bain de fusion et de créer des oxydes indésirables.

Un écoulement de gaz inadéquat provoque un cordon de soudure de mauvaise qualité dont la forme est irrégulière et très saillante. Des groupes d’éclats minuscules de matériau d’apport sont visibles (encerclés en rouge).
C’est le diamètre intérieur de la buse qui détermine le débit de gaz. S’il est de 15 mm, le débit sera de 15 l/min. Ce débit est généralement suffisant pour minimiser les éclats et éviter la formation de cordons de soudure épais. Il faut donc choisir la taille de buse en fonction de la taille de cordon de soudure souhaitée : une buse étroite donnera un cordon étroit; une buse plus grande donnera un cordon de soudure plus large. Le débit de gaz minimal requis pour effectuer une soudure est de 10 l/min.
L’avantage d’utiliser de l’oxygène comme gaz actif (technologie MAG) est une réduction de la teneur en carbone lors du soudage d’aciers comme les aciers 304L et 316L. Auparavant, un mélange gazeux contenant 2 % d’oxygène était utilisé à l’échelle mondiale. Cela dit, le soudage donnait un cordon noirci résistant au nettoyage. Aujourd’hui, ce mélange a été remplacé par un mélange à base de dioxyde de carbone. De nombreuses études confirment qu’une teneur en dioxyde de carbone inférieure à 5 % n’altère pas le pourcentage de carbone dans l’acier soudé. De plus, le gaz actif a une température basse, ce qui permet un soudage à faible apport de chaleur pour un cordon net et homogène.
Des mélanges spéciaux peuvent être obtenus en ajoutant de l’hydrogène. Pendant le soudage, l’hydrogène se lie à l’oxygène présent dans la zone de soudage et empêche l’oxydation du cordon. Pour éviter la fragilisation et les réactions chimiques violentes pendant le soudage, la teneur en hydrogène ne doit pas dépasser 2 %. L’hydrogène diminue la formation de silicates, crée un bain de fusion plus stable et réduit le temps et les dépenses nécessaires au nettoyage après le soudage. Ces mélanges ternaires sont adaptés à l’usinage de pièces d’une épaisseur de 4,5 mm. Les mélanges binaires produisent des résultats presque identiques lorsqu’ils sont utilisés avec des pièces de plus de 4,5 mm d’épaisseur.
L’épaisseur de la tôle affecte le procédé de soudage puisqu’une tôle plus épaisse contiendra plus de silicium qu’une tôle mince. L’épaisseur de tôle idéale est de 1 à 2 mm.
Paramètres électriques
L’augmentation de la tension augmente la température du bain de soudure et minimise donc la formation d’éclats. Lors du soudage à haute tension, un opérateur suffisamment compétent pour effectuer la soudure rapidement obtiendra un résultat impeccable, car le bain de soudure refroidit rapidement.
La formule suivante sert à calculer l’apport de chaleur (H) en fonction de la tension.

- V correspond à la tension d’arc (Volt)
- I correspond au courant d’arc (Ampère)
- ¿ correspond à l’efficacité du transfert de chaleur entre l’arc et le bain de soudure
- v correspond à la vitesse d’alimentation de la torche.
Lorsque la vitesse augmente, l’apport de chaleur diminue. La figure 4 montre comment une vitesse de soudage plus élevée produit une soudure plus fine et nette avec moins d’inclusions. Figure 4 shows how a higher welding speed produces a more restricted section and a lighter color with fewer inclusions.
Effet de la vitesse de soudage sur le cordon de soudure

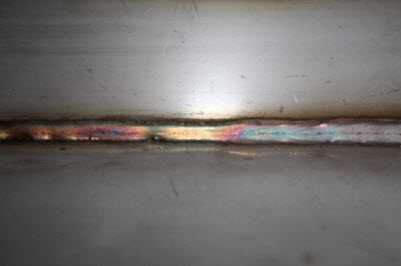
Si la vitesse de soudage est trop lente pour diminuer l’apport de chaleur, la valeur du courant diminue. Généralement, une augmentation de la tension permet d’obtenir une bonne soudure et d’éviter les projections et les éclaboussures. Comme le démontre la figure 5, un courant plus faible diminue l’apport de chaleur, ce qui entraîne la formation de silicates et des brûlures.


Figure 6 Cordon net, homogène et contrôlé obtenu à l’arc pulsé avec les paramètres électriques optimaux

Les vaporisateurs appliqués sur le métal de base sont souvent utilisés pour éviter la formation de projections. Cependant, ils détériorent la qualité de la soudure, car ils introduisent une substance qui provoque une réaction de combustion pendant le soudage, particulièrement lors du soudage à arc pulsé. La meilleure option consiste à utiliser des paramètres électriques correctement adaptés au débit du gaz, ce qui évite d’obtenir un cordon noirci, quelque peu aplati et entaché d’inclusions et de projections.


Comparativement au soudage à l’arc pulsé, le soudage MIG standard produit un cordon de soudure noirci et saillant, entaché d’une grande quantité de projections et d’inclusions d’oxyde. Plus la distance entre les bords est courte, plus ces défauts sont accentués.


Comparativement au soudage à l’arc pulsé, le soudage MIG standard produit un cordon de soudure noirci et saillant, entaché d’une grande quantité de projections et d’inclusions d’oxyde. Plus la distance entre les bords est courte, plus ces défauts sont accentués.
Pour les soudures plus larges, les rebords doivent être soudés par soudage à arc de pulvérisation (soudage MIG à tension élevée), en veillant à ce que la vitesse d’alimentation soit élevée. Vous obtenez alors l’apport de chaleur adéquat et les projections seront réduites, ce qui est non négligeable puisque ce type de soudage atteint une valeur de 220-230 ampères. Normalement, l’utilisation de systèmes automatiques peut aider à éviter ces problèmes.
Angle de la torche
Une opération de soudage effectuée dans les mauvaises conditions peut produire un cordon «¿collé¿». Dans ce cas, le cordon fait partiellement fondre le métal de base et flotte au-dessus de la soudure des rebords. La pièce peut alors subir une action mécanique qui provoque la destruction de la plaque de soudure et, éventuellement, la disjonction des deux bords. Un cordon de soudure triangulaire à angle de 45 ° doit alors être placé perpendiculairement entre les deux plaques.
Lors du soudage MIG, MAG et TIG, l’angle de la torche par rapport à la direction de la soudure a un impact important sur la forme du bain de soudure et le niveau de pénétration possible.
Figure 9: différents angles de la torche


La torche peut être inclinée ou bien perpendiculaire à la pièce à travailler. Une vitesse de soudage constante et une torche inclinée produiront un cordon de soudure net et homogène. Si la torche est tenue perpendiculairement, le cordon sera plus foncé et la zone affectée par la chaleur sera plus large.
Lorsque l’opérateur incline la torche dans la direction opposée au sens de la soudure (technique par tirage) — plutôt que dans la même direction — l’énergie de l’arc est concentrée dans le bain de fusion. Cette méthode entraîne une plus grande pénétration, un arc plus stable et moins de projections. Le fait d’incliner la torche dans la direction opposée à celle de la soudure obstrue la visibilité du bain. Cependant, à un angle de 25° (soudage à plat), le bain atteint normalement sa profondeur maximale.
Lorsque la torche est orientée dans la même direction que la soudure (technique par poussée), le bain de fusion perd en profondeur et les niveaux de pénétration et de dilution diminuent. Par contre, le bain est facilement visible et plus froid; il devient donc plus facile à contrôler.
La technique par poussée est préférable pour les applications manuelles. La torche doit être tenue à un angle de 5° à 15° pour diminuer le risque de défauts d’opération. Cependant, la technique de poussée ne peut être utilisée avec des fils fourrés qui produisent des scories, car leur intrusion entre le bain de soudure et l’électrode provoquerait l’extinction de l’arc. L’angle de la torche permet aux impuretés résiduelles de brûler avant que le bain de fusion n’atteigne la zone affectée, de sorte que les résidus ne sont pas incorporés dans la soudure. Un cordon de soudure MIG ou MAG ne sera net que si le soudage a été effectué à un angle interne et en respectant les paramètres appropriés. Dans ce cas, le gaz protecteur ne se disperse pas; il reste plutôt concentré dans la zone de travail.